Product Description
GOODA HL-12CNC


Model: HL-12CNC full-automatic high speed precision aluminum plate sawing machine
HL represents the model of the aluminum plate sawing machine from Heineda
2 represents the sawing capability of the aluminum plate saw machine:
the maximum sawing width of 3800mm
the maximum sawing height of 160mm(OP200mm)
the maximum sawing length of 3800mm
BNC represents the aluminum plate sawing machine is the full-automatic model.
CNC High Speed Circular Sawing machine is a machine that specialize in aluminum Square Bar be cut to pieces equipment. Applying mainly to sawing processing of aluminum alloy plates, the equipment has high reliability, high sawing efficiency, low operation cost, complete safety protection functions, sufficient static and dynamic rigidity and other significant characteristics. With the most advanced technology currently, it ensures the favorable dynamic quality of the system. The machine tool features simple utilization, operation and maintenance, appealing modeling and excellent after-sales service.
Design Concept & Functions:
1.The machinery framework is in the heavy-duty structure so that equipment enjoys stable operation.
2.The sawing foundation is in the lateral suspension structure; the quide device is arranged with
double-row roller type straight slide rail.
3.In the travelling of sawing foundation, the grinding gear, rack and servo motor are arranged to guarantee
the compatibility of sawing speed.
4.The pressing materials hood is in the overall design so that materials do not slide in the sawing.
5.The sucking pipe is reserved; large power dust collector is arranged.
6.Except for the floating rollers, all other contents on the working platform are made of chromium-plated
steel plate in order to avoid scratch of materials.
7.The suspended feeding clamp claw features as air pressure driving and clamping.
8.The driver of feeding mechanism is in the structure of servo motor + gear and rack.
9.The sawing foundation is elevated by hydraulic power; the ascending height of sawing blade is det up
according to the plate thickness.
10.The industrial computer and PC interface are arranged to set up parameters and control operation.
Execution standards of design and manufacture:
a. Design and manufacture of the equipment conform to ISO: 9001 international standard.
b. Design and manufacture of the equipment conform to CE standard certification.
c. Unit of measurement of all components and various instruments of the equipment adopt the international unit (SI) standard; main parts (include mechanical, electrical and electronic devices) of the equipment have reliable safety protection to prevent inaccurate operation or unexpected accident from damaging the machine.
I. Technical Specifications and Parameters
Model | HL-6BNC | |
Sawing capability | Cutting length | 3800mm |
Cutting width | 3800mm | |
Maximum cutting height | 160mm(OP200mm) | |
Maximum exposed height of saw blade | 165mm | |
Main saw blade | Main saw motor | 15KW |
Diameter of main saw | Ø550mm(OP630mm) | |
Diameter of main saw shaft core | Ø 38mm | |
Speed of main saw | 3900 r/min | |
Saw seat | Travel frequency conversion motor | AC 2.2KW |
Forward speed | Fastest 10m/min (load) | |
Backward speed | Fastest 22 m/min | |
Automatic feeding engine | AC 3KW | |
Utilization pressure | ≥5.0 kg/cm2 | |
Distance between working bench and floor | 1130 mm | |
Appearance size (L×W×H) of machine tool | 5900×6500×1980 | |
Voltage |
II. Mechanical Characteristics
1,Touch type operation monitor 1.1,.Touch type operation screen. 1.2 Several groups of working parameters can be set simultaneously to facilitate switching during sawing. 1.3 Guiding type input function. 1.4 Fault self-detection function. | ![]() |
2.1 Sizes to be cut can be input from the master control computer. An aluminum plates is fed from the front end of the equipment and clings to the front end of the feeder. Then the feeder clamps and pulls the plate in the machine automatically before automatic positioning. During sawing, the machine positions the plate to the set size automatically for sawing. The plate keeps its fixed status (the feeder ensures sufficient clamping strength and the hold-down beam compresses the plate tightly) all the time throughout the sawing process to ensure the sawing accuracy.
2.2 Bed rails at both sides of the feeding rack part consist of the welded steel beam structure. The hard chrome plating guide rail on the one side and the plane guide rail on the other side work with the gear wheel and gear rack for transmission, with magnetic ruler up to the accuracy in a dual-comparison mode. Besides, a reducer and 3 kilowatt servo motor are equipped for accurate and rapid driving and positioning. The sawing accuracy is ±0.2mm/m, feeding accuracy is ±0.1mm and repeat positioning accuracy is ±0.05mm.
3. Saw seat:
3.1. Ascending and descending type side suspension of the saw seat head adopts the design of up and down linear sliding rails in parallel to lower the moving inertia of the saw seat, improve the smooth moving of the saw seat and reduce the deflection shaking of the moving effectively to achieve the optimum linear accuracy of cutting.
4.2. 20HP (15 kilowatt) main saw motor features continuously variable speed, with the speed not less than 3900r/min. Travel of the saw seat adopt 3HP (2.2 kilowatt) frequency conversion motor to work with the reducer and the precision gear wheel and rack for transmission. The main saw works with the oil cylinder to move up and down. As a result, sawing is more powerful to avoid saw stuck, scrap squeezing and other phenomena generated by the traditional transmission mode of the chain.
4.3. Cutting positioning of the saw seat can edit and set the automatic positioning, ascending, cutting position and cutting start based on the program width. The saw bit moves below the working bench top. During sawing, the saw blade ascends from the bottom to the top. After one sawing, the saw blade descends below the working bench top automatically and returns to the plate end at the rapid feed speed to achieve the maximum production efficiency and protect the saw bit.
4.4. The square tubular dust collection groove is equipped below the saw seat, which is covered by rubber plates at both sides and stretches to the tail end of cutting to ensure the dust collection groove up to the maximum dust collection effect.
4.5. The maximum speeds of travel cutting and retreating of the saw seat are up to 10m/min and 22m/min separately. The sawing speed can be adjusted from the panel knob based on different heights of cutting work-piece, which can be changed during sawing. Users can adjust preference demands based on different properties of aluminum alloy plates to be sawn.
5. Main working bench:
The main working bench top is an air floating bench top, with air floating ball equipped on the panel with hard chrome plating. While enhancing the durability, it also improves the working efficiency of workers feeding plates.
6. The size of the feeding bench top with auxiliary air floating ball: L x W: 2100mm x 700mm, 3 PCS, steel surface structure; 2 bench tops are movable; steel rails are embedded in the floor to ensure smooth sliding of table tops after their installation. 3 bench tops can cling to each other for utilization. Bench tops can open and close the device of the air floating ball automatically based on the scope and position of the cutting. One end at the rear of each bench top is equipped with the roller. Load-bearing of each feeding bench top is higher than or equals to 3t. | ![]() |
7. Clamping claw: 7.1. Standard configuration of clip quantity: 12 clips, ensure long plate can be clamped normally after rotating for 90º; ensure the size accuracy, facilitate the operation and improve the efficiency. 7.2. Each clamping claw is equipped with the cylinder to clamp and pull work-piece plate in the lever mode. It ensures the working material clamps the plate reliably during clamping and pulling. 7.3. The maximum opening of feeding clamping claw: 170mm. | ![]() |
8. Dust-proof sheet The segment type dust-proof sheet adopts the transparent plastic sheet to restrain the powder ejection effectively and achieve the safety protection function. 9. Configuration of electrical control cabinet: 9.1. All electronic parts are purchased from the original manufacturer in Taiwan. 9.2. The servo motor and driver are from Japan Panasonic. 9.3. The frequency converter is from Taiwan . 9.4. Requiring no cooling system, electronic parts are popularized electronic accessories and can be purchased in the market for replacing. They only require regular cleaning and maintenance, without the trouble of dust invasion. | ![]() |
10. Power supply:
The power is three-phase industrial supply, with 380V/50HZ in the voltage.
11. Pressure supply:
Utilization pressure is 5 to 6 kg/cm2
12. Dust collection aperture:
Two dust collection pipe grooves locate at the front and back of the saw seat and one dust collection pipe groove locates above the cutting end, with three dust collection pipe grooves in total.
13. Standard configuration:
13.1. One main saw blade: tungsten carbide saw blade (Japan Kanefusa saw bit: φ550 in its diameter, with 60 teeth).
13.2. Clip: 12 PCS.
13.3. Floating feeding bench: 2100mm x 700mm x 3 sets.
13.4. The toolbox includes 1 group of tools.
13.5. One multi-rib belt of the main saw motor is equipped in the machine.
14. Sawing accuracy:
14.1 Linear accuracy of sawing is not less than ±0.2mm/m
14.2 Right angle accuracy of sawing is not less than ±0.2mm/100mm; perpendicular accuracy of sawing end face not less than ±0.05mm/100mm.
14.3 Size accuracy tolerance of sawing parts is ±0.2mm/m.
15. The maximum working noise of the equipment is ≤85dB.
16. Brands of main purchased parts
16.1 Schedule of main purchased parts
No. | Name | Model | Quantity | Brand | Place of origin |
1 | Main sawing motor | 15Kw | 1 set | Siemens | Germany |
2 | Feeding servo motor | AC-3KW | 1 PCS | Panasonic | Japan |
3 | Travel servo motor | AC-2.2KW | 1 PCS | Panasonic | Japan |
4 | Oil pump engine | 2.2KW | 1 PCS | Chyun Tseh | Taiwan |
5 | Shut-off check valve | KC-03 | 5 PCS | Seven Ocean | Taiwan |
6 | Solenoid valve | DSV-G02-22A | 2 PCS | Seven Ocean | Taiwan |
7 | Solenoid valve | DSV-G02-2C | 5 PCS | Seven Ocean | Taiwan |
8 | Solenoid valve | DSV-G02-6C | 2 PCS | Seven Ocean | Taiwan |
9 | Solenoid check valve | SV-08-20-DC24 | 1 PCS | Seven Ocean | Taiwan |
10 | AB end check valve | MPC-02-W-01-10 | 2 PCS | Seven Ocean | Taiwan |
11 | Hydraulic oil pipe | Customized | 1 set | Lianhuei | Taiwan |
12 | Hydraulic cylinder | Customized | 5 group | Heineda | China |
13 | Lubricating and cooling pump | Customized | 1 group | Dianhui | Taiwan |
14 | Oil pump | VPV40-70 | 1 PCS | Chyun Tseh | Taiwan |
15 | Linear guide rail | 45/35 | 4 group | Hiwin | Taiwan |
16 | Aluminum chip dust collector | 11KW | 1 group | Heineda | China |
17 | Programmable controller | OMRON | 1 set | CP1H | Japan |
18 | Frequency converter | 1 set | RM5G | Taiwan | |
19 | Travel switch | CA-2 | 1 1 set | OMRON | Japan |
20 | Transformer | 400VA | 1 set | CHNT | Domestic |
21 | Intermediate relay | RS2J | 1 set | IDEC | Taiwan |
22 | Electrical appliance components | 1 batch | Schneider | France |
16.2. Scope of supply and delivery of document and data
Main engine of sawing | 1 set | |
Plate hold-down device | Pneumatic | |
Feeding clip | 1 set | |
Anchor bolt and cushion block | 1 set | |
Spare parts and accessories | One batch (see packing list) | |
On-site installation | Buyer provides lifting equipment and common tools; supplier guides installation with buyer assistance | |
On-site commissioning | Supplier guidance | |
On-site training | Supplier takes charge of equipment operation, electrical principle and other necessary maintenance technical training | |
On-site acceptance | Responsibilities of both parties | |
Technical documents (delivered with equipment) | Certificate | One copy |
Operation instructions | One copy | |
Packing list | One copy |
FAQ:
1. What is your minimum order quantity and warranty?
MOQ is one set, and warranty is one year.
2.What CNC system do you use?
FANUC, SIEMENS, MISTSUBISHI etc. It depends on your choice.
3.When is the delivery time?
Conventional Machines,We will delivery then within 30-45 working days after received your
deposit,if some special machines will be some longer.we will give you the answer accordingly.
4. What is the package of the machines?
Packing: PE bag cover inside+ Plywood box + Steel beam frame.
5.How can I choose the most suitable machines ?
Please let us know your machining demand or machine size ,we can choose the best model
for you , or you can choose the exact model by yourself. You can also send us the products
drawing ,we will choose the most suitable machines for you .
6. What is your trade terms?
FOB, CFR,CIF or others terms are all acceptable.
7. What is your payment terms ?
Payment Terms : T/T 30% advance , 70% before shipment.
Products & Concept
Company Profile
We are the manufacturer to produce the high-end CNC machine in China, who focusing on developing and supplying the high efficiency, high accuracy, and high quality of CNC Duplex Milling Machine, Exchange-Pallet Vertical CNC Milling Machine,CNC Gantry Grinding Machine,5-Axis High Speed Gantry Machining Center , CNC High Speed Saw Machine and CNC Chamfering Machine.
Our aspiration is to be flexible in implementing customer requirements, guarantee the high reliability of the milling machine, ensure that spare parts are available at short notice and facilitate the prompt availability of service engineers.
GooDa's five factories in China
Cooperative Partner
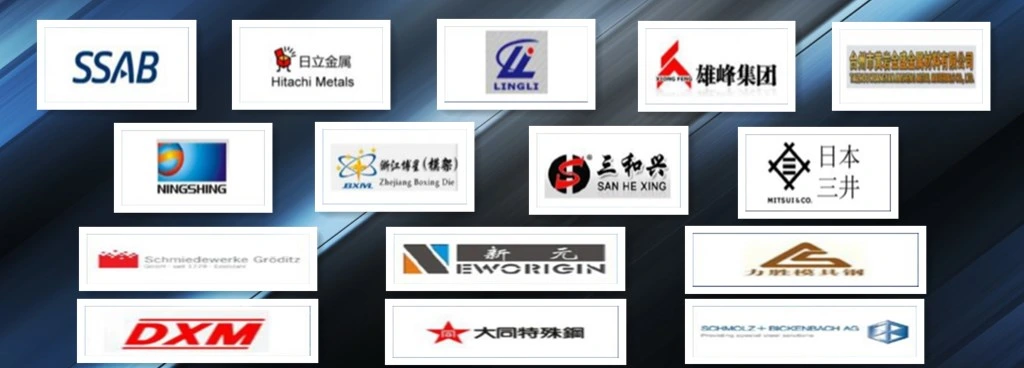
Maintenance & Service
The benefits of GOODA maintenance contract (After sales 3 years):
- Basic requirement in a certified QS system
- Guarantee for the accuracy of the measuring and test results
- Calibration, maintenance and, if necessary, repair with just one visit
- Fixed prices with a clear breakdown of costs
- Preventive maintenance helps you avoid expensive faults and ensures a high level of quality that lasts
The maintenance contract includes:
- Travelling time and expenses for our technician
- Maintenance and calibration work
- Small items required for carrying out the specified maintenance work
- Calibration with a corresponding maintenance and test report, allowing the results to be used to demonstrate compliance with national standards
Dongguan GooDa Machinery Manufacturing Co., Ltd.
HEAD ADD: Head office: 216,Huanchang North Road, Changping Town, Dongguan City, Guangdong Province.
Please contact:
Una