Product Description
UNS S17700 (17-7PH, AISI 631) semi-products for stainless elastic element, engine thrust unit component, ship shaft
1 PRODUCT
UNS S17700 (17-7PH, AISI 631) semi-products for stainless elastic element, engine thrust unit component, ship shaft etc.
UNS S17700 is available in product forms as plate, sheet, strip, pipe, tube, bar (round, flat, hexagon, square, shapes), wire (profile, round, flat, square), forgings, etc.
2 EQUIVALENT DESIGNATION
07Cr17Ni7Al(GB/T), 17-7PH,AISI 631(ASTM), SUS 631(JIS), W.Nr. 1.4568, ATI 17-7™
3 APPLICATION
UNS S17700 provides valuable property combinations particularly well suited for aerospace and many spring type applications requiring high strength.
This special alloy also provides benefits for other applications requiring formability, high strength and good corrosion resistance, as well as excellent properties for flat springs, belleville (conical spring) washers, stainless elastic element, eyelets, clips, surgical parts, blades, bellows, honeycomb, engine thrust unit component, membrane, ship shaft, compressor disc and strain gauges at temperatures up to 600°F (316°C).
4 OVERVIEW
S17700 stainless steel is a semi-austenitic chromium-nickel-aluminum precipitation-hardening stainless steel that provides high strength and hardness, excellent fatigue properties, good corrosion resistance and minimum distortion upon heat treatment. It is easily formed in the annealed condition, then hardened to high strength levels by simple heat treatments to Conditions RH 950 and TH 1050. The exceptionally high strength of Condition CH 900 offers many advantages where limited ductility and workability are permissable.
In its heat-treated condition, this alloy provides exceptional mechanical properties at temperatures up to 900°F (482°C). Its corrosion resistance in both Conditions TH 1050 and RH 950 is superior to that of the hardenable chromium types. In some environments, corrosion resistance approximates that of the austenitic chromium nickel stainless steels. In Condition CH 900, its general corrosion resistance is comparable to that of Type 304. Fabricating practices recommended for other chromium-nickel stainless steels can be used for this material.
In addition to material produced by the standard refining procedures, material which has been vacuum arc or electroslag remelted is available for further increase in resistance to fatigue, for those applications subject to cyclic stresses.
5 CHEMICAL COMPOSITION (wt%):
Fe | Ni | Al | Cr | Cu | C | Mn | Si | P | S |
Balance | 6.50-7.75 | 0.75-1.50 | 16.0-18.0 | ≤0.50 | ≤0.09 | ≤1.00 | ≤1.00 | ≤0.040 | ≤0.030 |
6 PHYSICAL PROPERTY
Physical properties | Condition | ||||
A | TH 1050 | RH 950 | CH 900 | ||
Density | lbs./in3. (g/cm3) | 0.282 (7.81) | 0.276 (7.65) | 0.276 (7.65) | 0.277 (267) |
Modulus of elasticity | ksi. (GPa) | - | 29.0 x 103 (200) | 29.0 x 103 (200) | - |
Electrical resistivity | µΩ•cm | 80 | 82 | 83 | 83 |
Magnetic permeability H/m | @ 25 oersteds | 1.4 - 3.4 | 132 - 194 | 82 - 88 | - |
@ 50 oersteds | 1.4 - 3.6 | 120 - 167 | 113 - 130 | - | |
@ 100 oersteds | 1.4 - 3.5 | 80 - 99 | 75 - 87 | 70 | |
@ 200 oersteds | 1.4 - 3.2 | 46 - 55 | 44 - 52 | 43.5 | |
Maximum | 1.4 - 3.6 | 134 - 208 | 119 - 135 | 125 | |
Thermal conductivity, BTU/hr./ft2./°F (W/m/K) | 300 °F (149 °C) | - | 117 (16.9) | 117 (est) (16.9) | 114 (16.4) |
500 °F (260 °C) | - | 128 (18.5) | 128 (est) (18.5) | 127 (18.3) | |
840 °F (449 °C) | - | 146 (21.1) | 146 (est) (21.1) | 150 (21.6) | |
900 °F (482 °C) | - | 146 (21.1) | 146 (est) (21.1) | 151 (21.8) | |
Mean coefficient of thermal expansion in./in./°F (μm/m/K) | 70 - 200 °F (21 - 93 °C) | 8.5 x 10-6 (15.3) | 5.6 x 10-6 (10.1) | 5.7 x 10-6 (10.3) | 6.1 (11.0) |
70 - 400 °F (21 - 204 °C) | 9.0 x 10-6 (16.2) | 6.1 x 10-6 (11.0) | 6.6 x 10-6 (11.9) | 6.2 (11.2) | |
70 - 600 °F (21 - 316 °C) | 9.5 x 10-6 (17.1) | 6.3 x 10-6 (11.3) | 6.8 x 10-6 (12.2) | 6.4 (11.5) | |
70 - 800 °F (21 - 427 °C) | 9.6 x 10-6 (16.0) | 6.6 x 10-6 (11.9) | 6.9 x 10-6 (12.4) | 6.6 (11.9) |
7 MECHANICAL PROPERTIES
Typical room temperature mechanical properties
Property | Condition | |||||||||||||||
A | T | TH 1050 | A 1750 | R 100 | RH 950 | C | CH 900 | |||||||||
UTS, ksi. (MPa) | 120 | (827) | 145 | (1000) | 200 | (1379) | 133 | (917) | 175 | (1207) | 230 | (1586) | 230 | (1586) | 295 | (2034) |
0.2% YS, ksi. (MPa) | 45 | (310) | 100 | (690) | 185 | (1276) | 42 | (290) | 115 | (793) | 210 | (1448) | 190 | (1310) | 275 | (1896) |
Elongation % in 2" | 35 | 9 | 8 | 19 | 9 | 7 | 5 | 2 | ||||||||
Rockwell Hardness | B85 | C31 | C43 | B85 | C37 | C48 | C44 | C52 |
8 CORROSION RESISTANCE
Corrosion resistance of S17700 stainless steel in Conditions TH 1050 and RH 950 is generally superior to that of the standard hardenable chromium types of stainless steels such as Types 410, 420 and 431, but is not quite as good as chromium-nickel Type 304. Corrosion resistance in Condition CH 900 approaches that of Type 304 stainless steel in most environments.
Stress cracking in marine environments
The precipitation-hardening stainless steels, like the hardenable chromium stainless steels, may be subject to stress corrosion cracking when stressed and exposed to some corrosive environments. The tendency is related to the type of stainless steel, its hardness, the level of tensile stress and the environment.
Stress cracking tests on the precipitation- hardening alloys has been conducted in a marine atmosphere 82 ft. (25 m) from the waterline using two-point loaded bent-beam specimens.
Data reported here are the results of multiple specimens exposed at stress levels of 50 and 75% of the actual yield strength of the materials tested. Test specimens were 0.050 in. (0.127 mm) thick heat treated to Conditions TH 1050 and RH 950. Specimens in Condition CH 900 were 0.041 in. (1.04 mm) thick. The long dimension of all specimens was cut transverse to the rolling direction.
When comparing the various heat-treated conditions, the data show that S17700 stainless steel has the greatest resistance to stress cracking in Condition CH 900. Likewise, Condition TH 1050, although somewhat less resistant than Condition CH 900, appears to be more resistant to stress cracking than Condition RH 950.
Table 8-1 summarizes the test data. In addition, in the mild industrial atmosphere, specimens stressed at 90% of their yield strength had not broken after 730 days of exposure.
Table 8-1 Summary of stress-cracking tests in coastal exposure
Heat Treatment | Stressed at 50% of the 0.2% Yield Strength | Stressed at 50% of the 0.2% Yield Strength | ||||
Stress, ksi. (MPa) | Days to Failure | Range Days | Stress, ksi. (MPa) | Days to Failure | Range Days | |
TH 1050 | 100.8 (694) | No failures in 746 days | - | 151.3 (1043) | 100 (2)** | 82 - 118*** |
TH 1050 | 89.0 (614) | No failures in 746 days | - | 133.6 (921) | No failure in 746 days | - |
RH 950 | 111.6 (769) | 30.2 | 16 - 49 | 167.5 (1154) | 7.4 | 6 - 10 |
RH 950 | 110.2 (759) | 116(1)** | - | 165.4 (1141) | 51.6 | 26 - 71 |
CH 900 | 142.8 (986) | No failures in 746 days | - | 214.2 (1476) | No failures in 746 days | - |
9 HEAT TREATMENT
S17700 stainless steel requires three essential steps in heat treating:
1) Austenite conditioning
2) Cooling to transform the austenite to martensite
3) Precipitation hardening
Standard heat treatments
It presents the procedures for heat treating material in condition A to conditions TH 1050 and RH 950.
Condition A
For in-process annealing (mill annealing), the alloy should be heated to 1950 ± 25°F (1066 ± 14°C) for three minutes for each 0.1 in. (2.5 mm) of thickness, and air cooled. This treatment may be required to restore the ductility of cold-worked material so that it can take additional drawing or forming. Although most formed or drawn parts do not require
re-annealing prior to hardening, annealing is required on severely formed or drawn parts to be heat treated to Condition TH 1050 if full response to heat treatment is required. Annealing is unnecessary in the case of the RH 950 heat treatment.
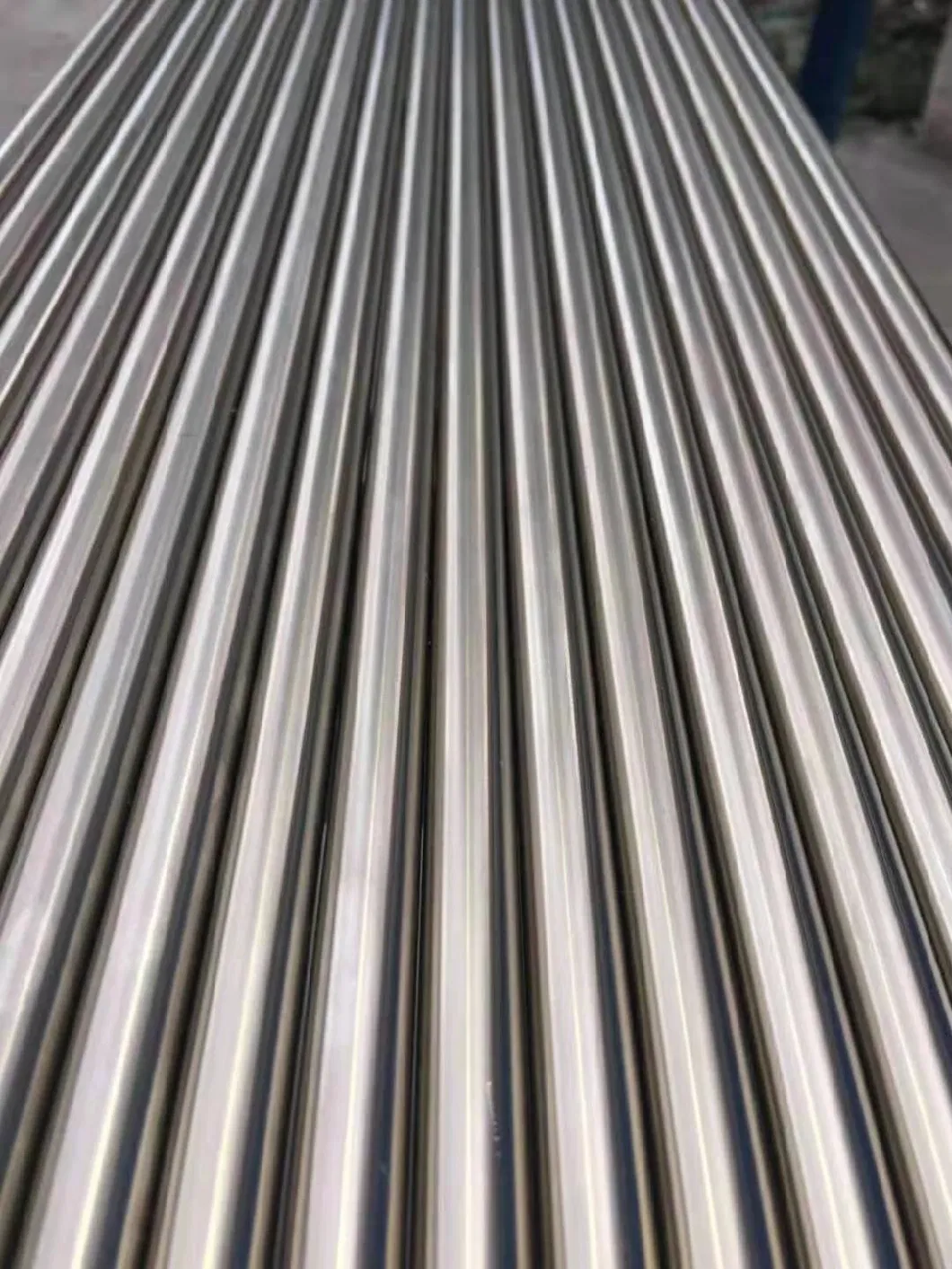
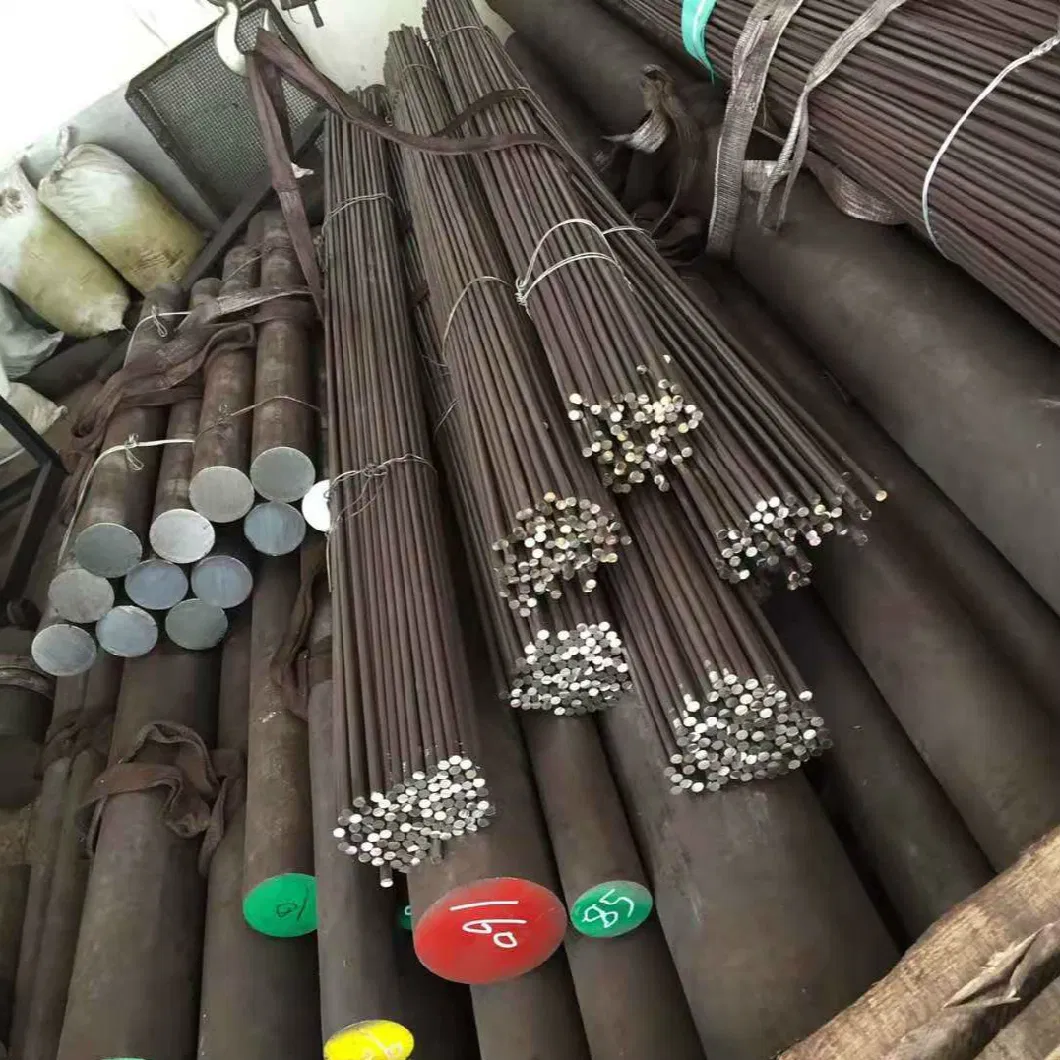
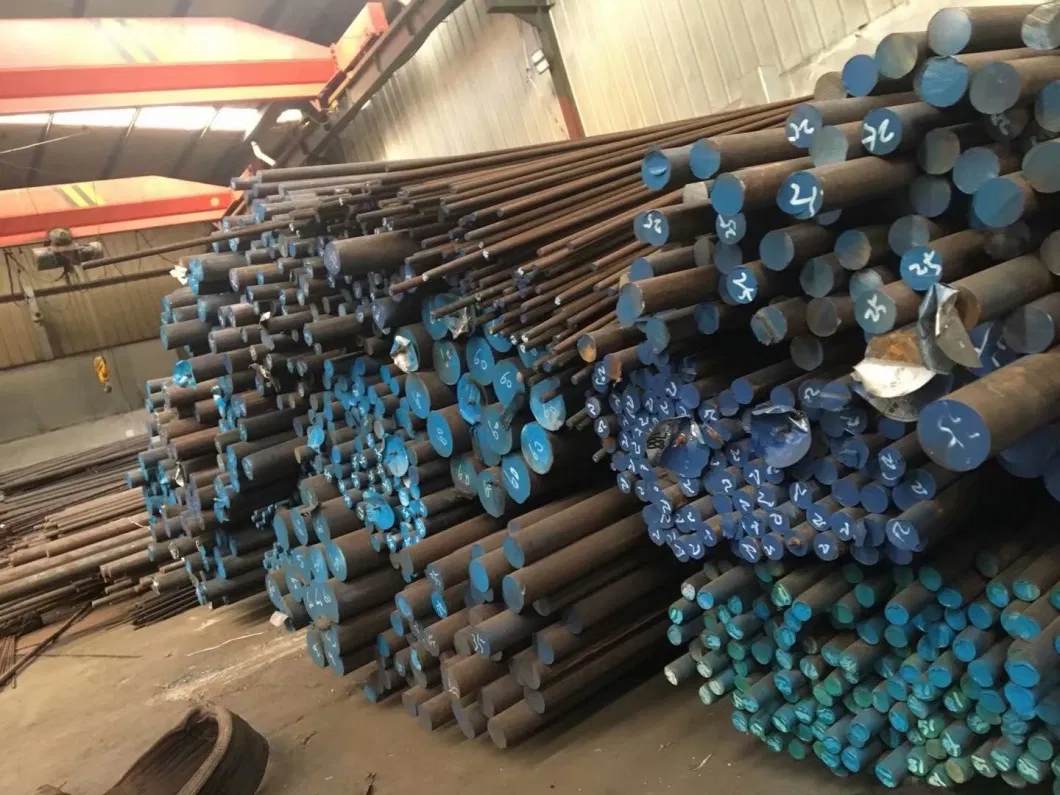
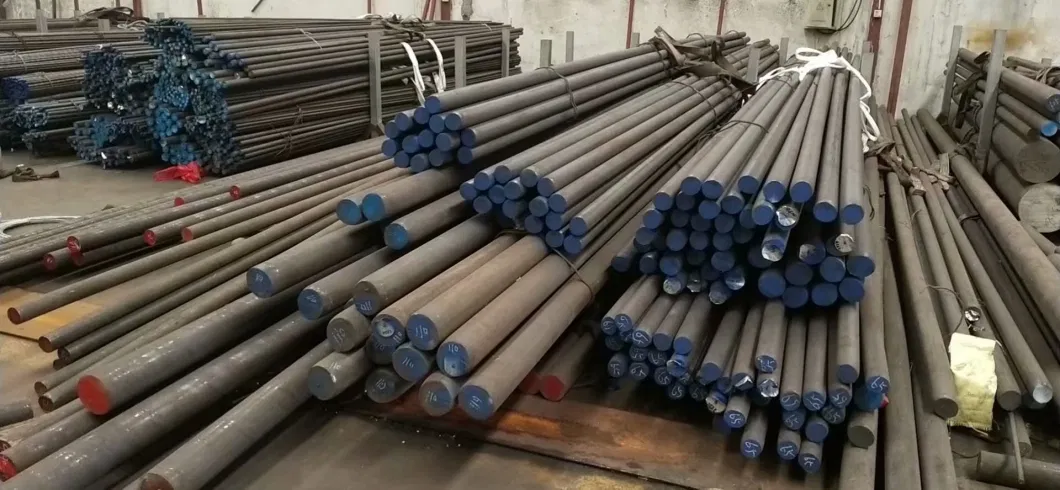
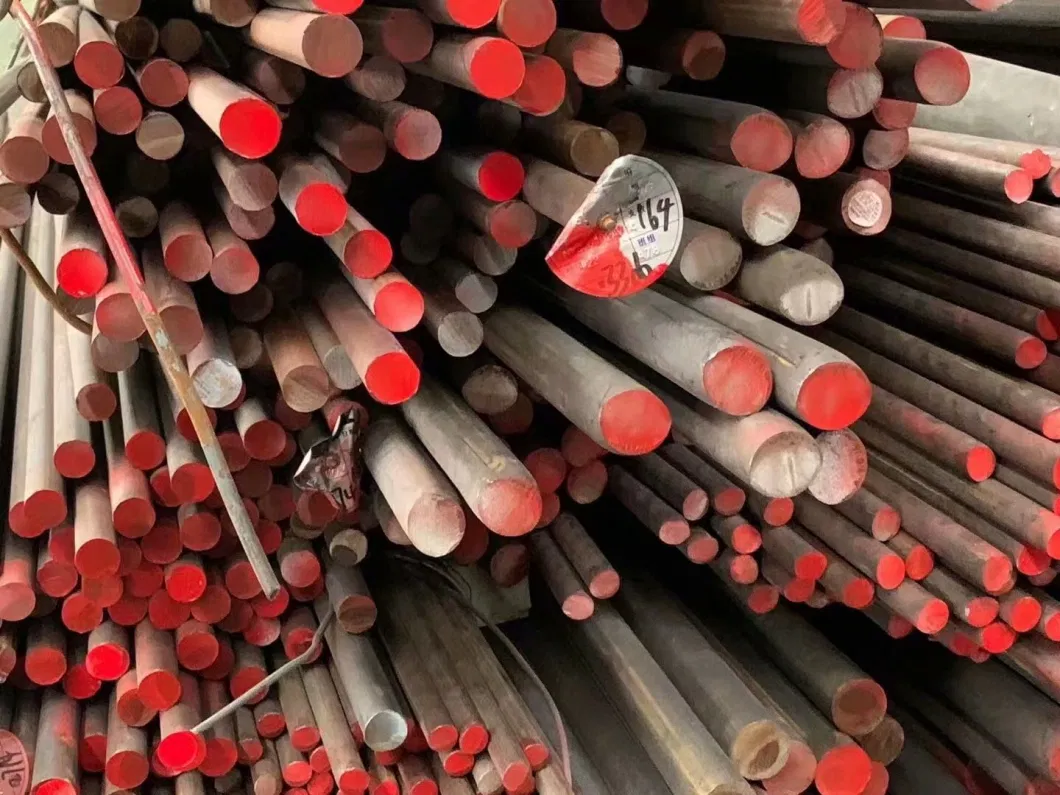